Waiting for the present to catch up the future
A better test of lithium-ion battery aging waited nearly a decade before anyone asked for it
Waldemar Weber
Shimadzu Europa GmbH
Ever had a good idea that no one else seemed to care about? Sure, we all have. People are busy, and even the best answer in the world may pass us by if the question it answers isn’t one we are currently asking. Some people actually have jobs where they are supposed to go searching for answers to questions no one else is asking. People such as scientists, and scientists such as Waldemar Weber.
Weber is an expert researcher in gas chromatography/mass spectrometry (GC-MS) at Shimadzu Europa. He spends his time exploring new laboratory applications for the powerful, versatile analytical tool that GC-MS provides. He also has a keen interest in battery technology, and one day he became curious about whether he could use GC-MS to better test rechargeable lithium-ion batteries for aging – meaning how long they would last.
As scientists do, he tinkered with his idea and rigorously tested it out in his lab over two years and, finally, wrote it all up and published it. The method worked amazingly well, and surely industry would now leap up and begin using it to improve their products and their bottom lines. There was only one problem: It was 2015. No one cared.
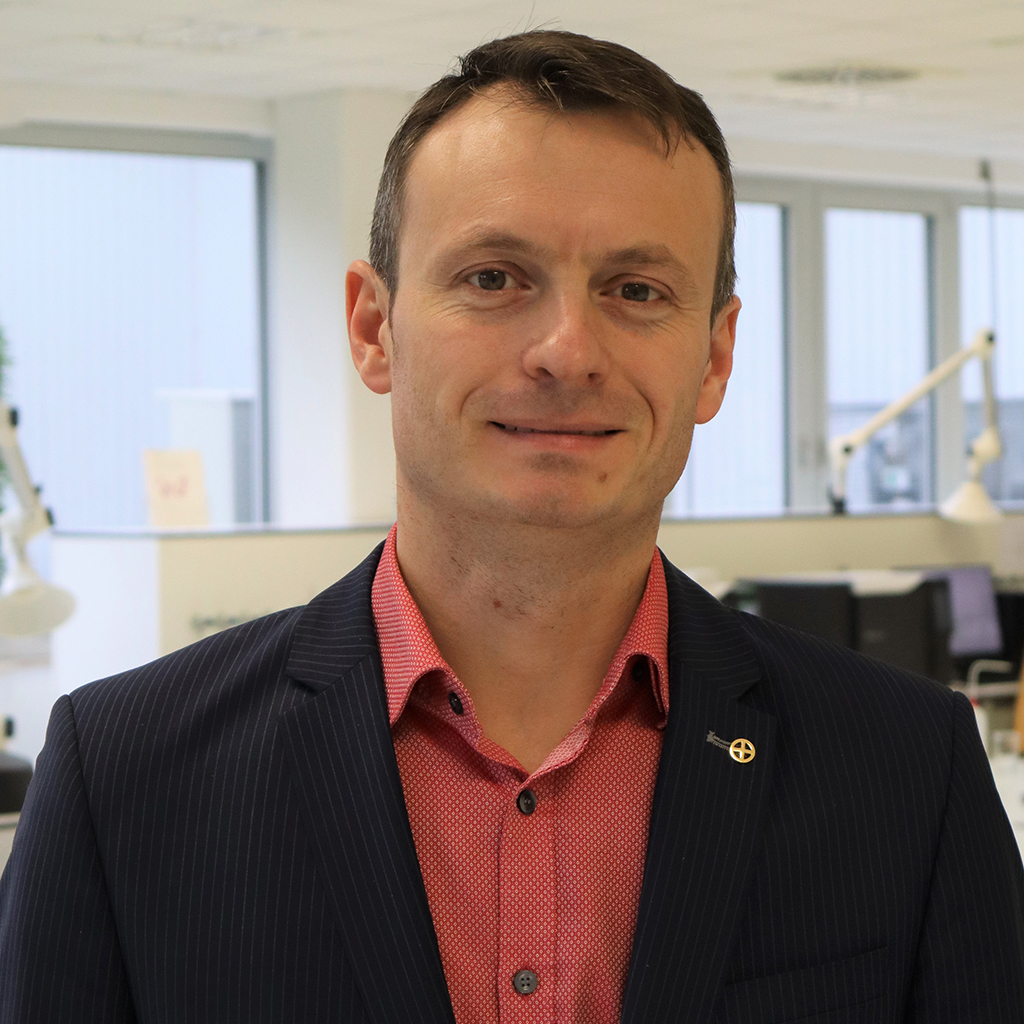
What a difference a decade makes
Flash forward to 2024: Since 2015, the market for batteries – and rechargeable lithium-ion batteries (LIBs) in particular – has skyrocketed, creating a self-reinforcing cycle of innovation, lower prices, greater capacity, higher safety and better performance. Much of the impetus behind this has been the dramatically growing interest in sustainability.
The rapidly expanding global market for electric vehicles (EVs) is a perfect example: EVs not only bypass the harmful tailpipe emissions of internal-combustion engines but also allow for the use of sustainably produced energy to power them. And at the heart of any EV – as well as everything from laptops and smartphones to e-bikes, digital cameras and portable power drills – is the rechargeable battery.
Like most things, batteries don’t last forever – even rechargeable ones. Batteries naturally lose capacity as they age, and factors such as temperature, usage and even battery design will affect how a battery ages. Batteries which have aged significantly lead (for instance) to a reduced range of distance for an EV between charging. At the same time, increases in battery-internal resistance over time result in less power: Acceleration of an EV becomes slower.
Strengthening the weakest link
As important as they are, batteries are sometimes referred to as the weakest link in the electronics at the heart of the modern world. Battery science attempts to design better batteries, for instance ones which degrade less slowly and last longer. So, testing batteries is therefore of central importance to any industry that relies on them in its products or processes. One of the key purposes of testing: How long will this battery last?
That is not a simple question. Easy and quick testing models do exist, but their abilities are more or less limited to identifying whether a particular battery is inherently substandard or not. There are also more complex, time-consuming models, but even with an array of expensive equipment, this type of testing is often of the trial-and-error variety.
Batteries are more complicated than you might think
Better ways to test battery aging would result in greater predictability of how long a battery could be expected to last as well as point toward ways in which an individual type of battery might be made to perform more efficiently and effectively for a longer period of time. So, the stakes are high! And, given both the complexity of the challenge and the importance of answer, researchers have been hard at work looking for answers. Batteries are complicated. But, for scientists like Waldemar Weber, that’s half the fun!
Waldemar Weber began by thinking about the electrolyte solution, which is a crucial part of a typical lithium-ion battery – the most popular rechargeable battery chemistry – consisting of Li salts (e.g. LiPF6) and organic carbonates. Decomposition is a continuous chemical process, and the formation of phosphorous-based and other organic products starts already at the production stage of the electrolyte. The formation of such molecules does not affect the electrolyte/battery quality negatively, as long as the quantity is low enough. On the contrary, several decomposition products have a positive effect on the formation of the so-called SEI surface (Solid Electrolyte Interface) on the LIB anodes, which is crucial for battery functionality. Thus, the increasing amount of some of the decomposition products is a clear indicator of the progressive aging of the battery/electrolyte.
Could GC-MS simplify the analysis of electrochemical aging?
Weber was curious to know whether GC-MS was suitable for investigating the aging of LIBs using phosphate-based degradation products – specifically trialkyl phosphates – typically produced as reaction products of carbonates and LiPF6 salt. He reasoned that these compounds could be used as markers for electrochemical battery aging because of their slow formation and limited dependence on only a few external parameters. This might allow the investigation of electrochemical aging (charge/discharge) by a simple comparison of before/after analyte content.
The decomposition of LiPF6 salts under reaction with traces of water and the corresponding electrolyte solvent can be influenced by electrochemical and chemical processes. The formation of tri-alkylated species can be described by a simplified reaction sequence shown in Figure 2. The non-, mono- and di-alkylated phosphates shown in step 1 and step 2 are usually detectable even in new LIB electrolytes. These reactions happen very quickly. The content observed is, therefore, significantly higher in comparison to the tri-alkylated species shown in step 3. Due to the fact that the tri-alkylated species are formed very slowly through the reaction of organic carbonates with conductive salts, they can be very useful indicators for battery aging.
Using samples provided by the MEET Battery Research Center at the University of Münster (Germany), electrolytes from commercially available 18650 LIBs were investigated. One of the batteries was new, while the other was charged/discharged at 40 °C, with cycling stopped at a remaining discharge capacity of 70 % (around 1,500 cycles). After that, both batteries were opened, and the jelly roll (aka Swiss roll: the design used in the majority of cylindrical rechargeable batteries) was extracted using supercritical fluid extraction (SFE) and acetonitrile as cosolvents. Before the injection of 1 µL, the extract was dissolved with dichloromethane (DCM) 1:10.
To analyze the phosphate species, Weber used the scan mode on a Nexis GC-2030 with a GCMS-QP2020 NX (gas chromatograph plus mass spectrometer detector). This enabled the identification of the different analytes based on their spectra. Since most compounds were not available in the most common libraries, the spectra from available scientific publications were used as a reference.[1]
The corresponding retention times used m/z traces, the detected areas of the different compounds being summarized in Table 1. The fluorinated species could be found in both the new and the aged battery. The content of ethyl methyl fluorophosphate (EMFP) and diethyl fluorophosphate (DEFP) in the aged battery is significantly higher than in the new one, and at the same time the content of dimethyl fluorophosphate (DMFP) is slightly lower. The reason for this result is the very fast formation of fluorinated compounds and their dependence on many external factors (sample preparation, time of storage, moisture).
As mentioned above, the fluorinated compounds are more suitable to analyzing the quality of the manufactured electrolyte, e.g. to investigate the destruction due to storage conditions like moisture levels. In contrast to the fluorinated compounds, the tri-alkylated phosphates are formed significantly slower and are usually not detectable in a fresh electrolyte, offering the possibility of using their formation as an indicator of battery aging.
The GC-MS chromatograms thus obtained and the corresponding MS spectra are shown in Figure 3. As indicated in Figure 4, trimethyl phosphate (TMP), ethyl dimethyl phosphate (EDMP) and diethyl methyl phosphate (DEMP) could be detected in the electrolyte after 1,500 charge cycles. Triethyl phosphate (TEP) was not observed in this experiment, however TEP might be detected in a sample with a more advanced aging.
An idea whose time has come
In 2015, Weber was successful in proving that gas chromatography/mass spectrometry using scan measurements of phosphate-based degradation products offers a simple and effective new method for the quality control of battery aging. Companies and research institutions wishing to apply this method to their own needs are encouraged to do so. Weber also suggests that using a scan/SIM mode would be beneficial, as it provides the opportunity of detecting the main compounds (carbonates, additives) and the degradation products in one measurement. Also, that using a dedicated SIM method for the phosphates with the highest selectivity and sensitivity would be advantageous.
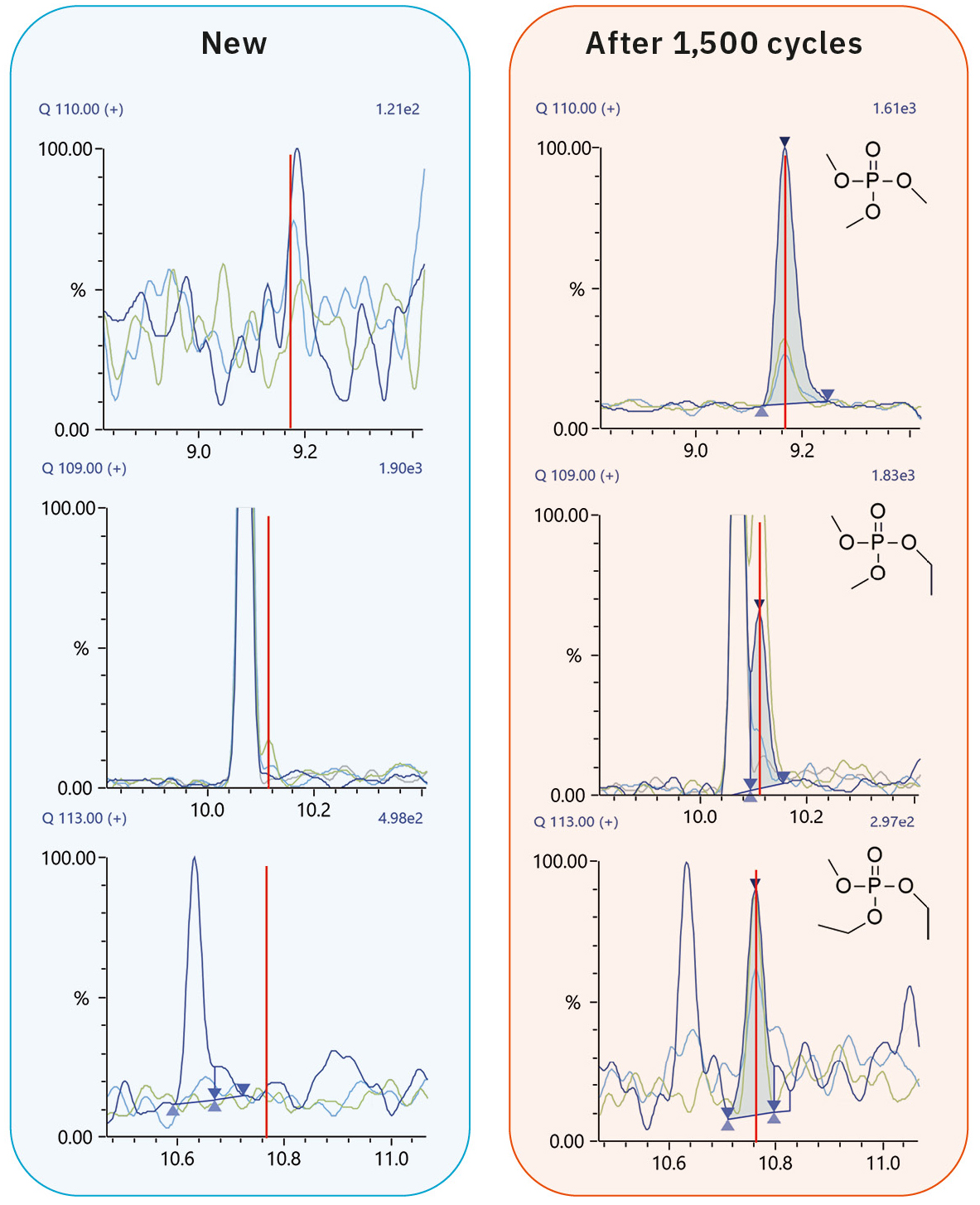
Better battery testing is good for business, consumers and the planet
On the frontiers of science, working together is the best way to not only survive but to prosper. Being able to better test how and how much a battery ages will be of immense value in ensuring that battery technology continues to evolve and spread its benefits. And – in whatever field we may find ourselves – it’s important to remember that patience pays off and that a good idea is never wasted. Better ways of doing things eventually win out over traditional ways. Even if there are occasional delays.
Peak area | |||||
Compound |
Chemical |
m/z |
Ret. |
New |
After 1500 |
Dimethyl fluorophosphate (DMFP) |
![]() |
97, 98, 128 |
3.83 |
15304 |
11406 |
Ethyl methyl fluorophosphate (EMPF) |
![]() |
97, 115, 127, 141 |
5.64 |
7015 |
14619 |
Diethyl fluorophosphate (DEPF) |
![]() |
101, 113, 129 |
8.05 |
2136 |
3426 |
Trimethyl phosphate (TMP) |
![]() |
140, 110, 109, 95 |
9.12 |
N.D |
3952 |
Ethyl dimethyl phosphate (EDMP) |
![]() |
153, 139, 127, 110, 109, 96, 95 |
10.11 |
N.D |
1028 |
Diethyl methyl phosphate (DEMP) |
![]() |
141, 113 |
10.77 |
N.D |
588 |
Triethyl phosphate (TEP) |
![]() |
155, 127, 109, 99 |
N.D |
N.D |
N.D |
Equipment used by Waldemar Weber
The recommended analytical hardware and software configuration is listed below.
Main unit: Nexis GC-2030 with GCMS-QP2020 NX: gas chromatograph plus mass spectrometer detector
Accessory: AOC-30i autosampler
Main consumables: SH-I-5MS, 30 m × 0.25 mm × 0.25 μm; P/N 221-75940-30
Software: GCMSsolution and LabSolutions Insight
A picture of the instrument used, including the main unit and the accessory, can be seen in Figure 1.
[1] Weber W., Kraft V., Grützke M., Wagner R., Winter M., Nowak S. (2015). Identification of alkylated phosphates by gas chromatography–mass spectrometric investigations with different ionization principles of a thermally aged commercial lithium-ion battery electrolyte. Journal of Power Sources. 1394: 128–136