Not a gray area: Meeting the challenge of sustainable hydrogen generation
UK-based start-up aiming to produce
carbon-negative hydrogen
Dr. Michael Sims, Wild Hydrogen
The potential of hydrogen as an environmentally benign fuel is only to be realized if it can be turned cost-effective and if society is able to move away from the current market dominance of “gray hydrogen” and its unsustainable CO2 emissions. Pyrolysis of biomass has been well studied as a potentially carbon-neutral way of making hydrogen, but it’s tended to require extensive feedstock processing and high energy use. Now, however, the UK-based start-up Wild Hydrogen thinks they’ve overcome all these problems with a new design of gasification reactor. We talk to them about how they plan to make hydrogen generation carbon-negative and how they’re using Shimadzu’s GC-MS to understand the composition of their gaseous, liquid and solid products.
Gray, blue, green … and clear
The global hydrogen market is currently worth £100 billion, with key target applications being in sectors that are hard to convert to electrical energy, such as heavy industry, and as a fuel for goods vehicles and shipping.
But there’s a big problem with hydrogen – and that’s the way it’s generated. The market is currently dominated by gray hydrogen, which is made by gasifying fossil fuels but emits lots of CO2 in the process. Blue hydrogen, generated the same way but with carbon capture and storage, is resource-intensive and thus very expensive. And green hydrogen, produced by electrolysis of water with electricity from renewable sources, has the same problems and uses scarce materials too, making it uneconomic.
So, how can we make hydrogen production both less resource-intensive while at the same time eliminating – or even reversing – the CO2 emissions that typically accompany it? The R&D company Wild Hydrogen thinks it has the answer, and they’re using a Shimadzu GC-MS to help them on their journey to what they call “Clear Hydrogen”.
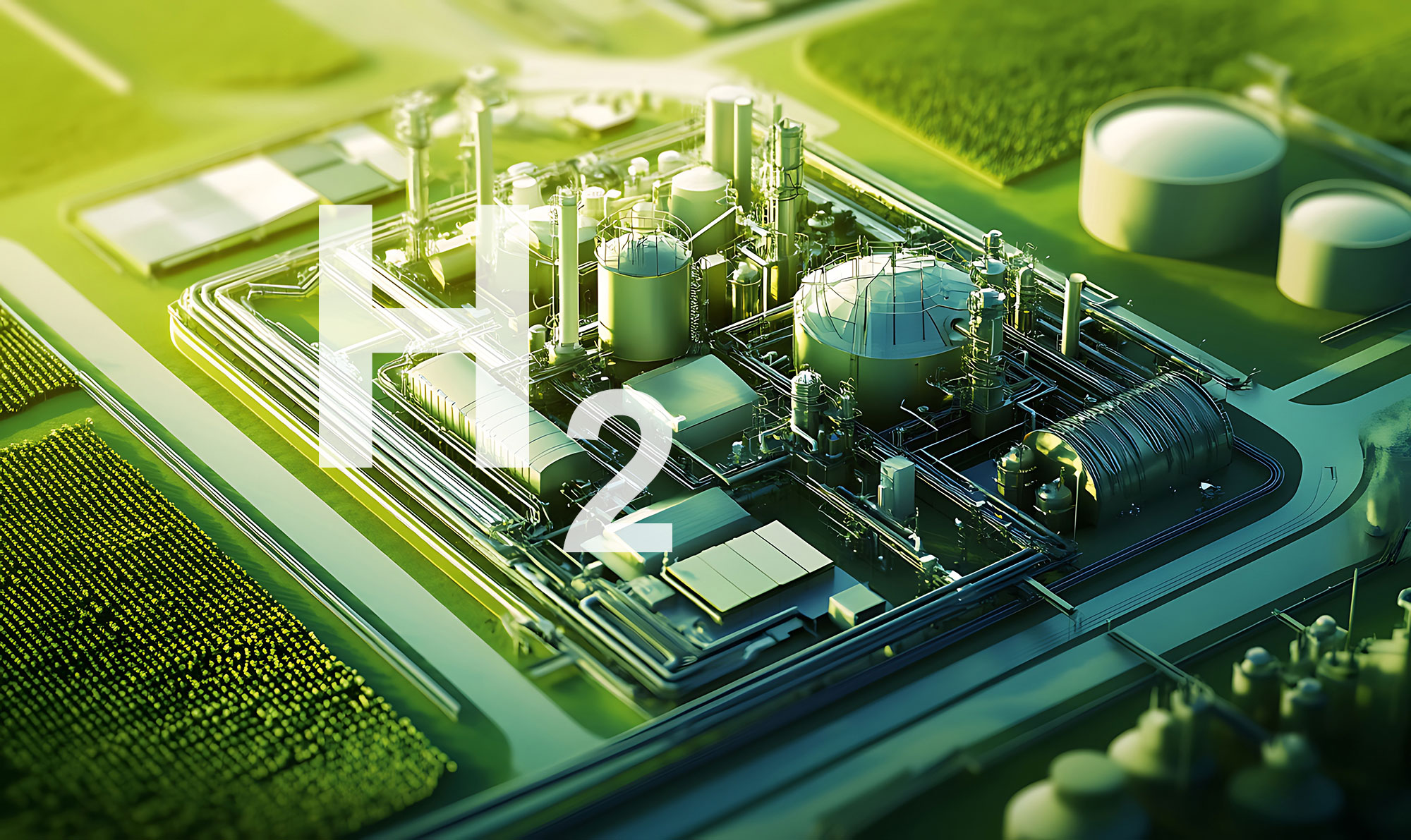
Adding carbon capture to biomass gasification
Wild Hydrogen was conceived over a coffee shop conversation between James Milner (now CEO) and Mark Wickham (now CTO) in October 2021. “The name came from our commitment to technological innovation in hydrogen production and a bold willingness to challenge the status quo in the evolving energy landscape,’’ says James Milner. A few months later, the company was founded, and a collaboration was set up with Cranfield University and Helical Energy to help bring their idea to fruition.
That idea centers on the gasification of biomass into hydrogen and CO2, using a reactor-based process that effectively has the capabilities to remove atmospheric CO2 by capturing it from the produced gas stream. Because the feedstock is not derived from fossil carbon and because the CO2 can be captured, this method is potentially not just carbon-neutral but carbon-negative. So, at a stroke, it would generate the hydrogen needed for tomorrow’s economy while also (in effect) using photosynthesis to do the difficult work of removing CO2 from the atmosphere, which is driving climate change.
With their work still in the development phase, the details of their reactor and the process they use are not yet in the public domain. They’ve made three major advances that have enabled them to make the production of hydrogen economically viable:
- Minimal pre-preparation: Their method does not require extensive processing of the feedstock prior to introduction into the reactor. Specifically, the biomass can have a water content as high as 50 wt% and doesn’t need to be milled to a uniform size, boosting the overall cost-effectiveness.
- Reduced heating cost: By careful reactor setup and workflow, they’ve been able to reduce the amount of time and energy needed to raise the biomass to the temperature and pressure needed for gasification.
- Minimal use of resources: By using only readily available metals and ceramics, their approach eliminates the need for scarce or hazardous rare earth metals. Unlike some other methods, large amounts of water are also unnecessary, further enhancing the method’s green credentials.
To demonstrate that their concept works in practice, the team at Wild Hydrogen has been busy developing a series of prototypes over the last two years, which have steadily increased in scale, efficiency and robustness. Their reactor design has also been shown to work with a variety of different biomass feedstocks, including bioenergy crops, forestry residues, macro-algae as well as waste products such as oversized compost. The reactor even gives good results with waste plastic!
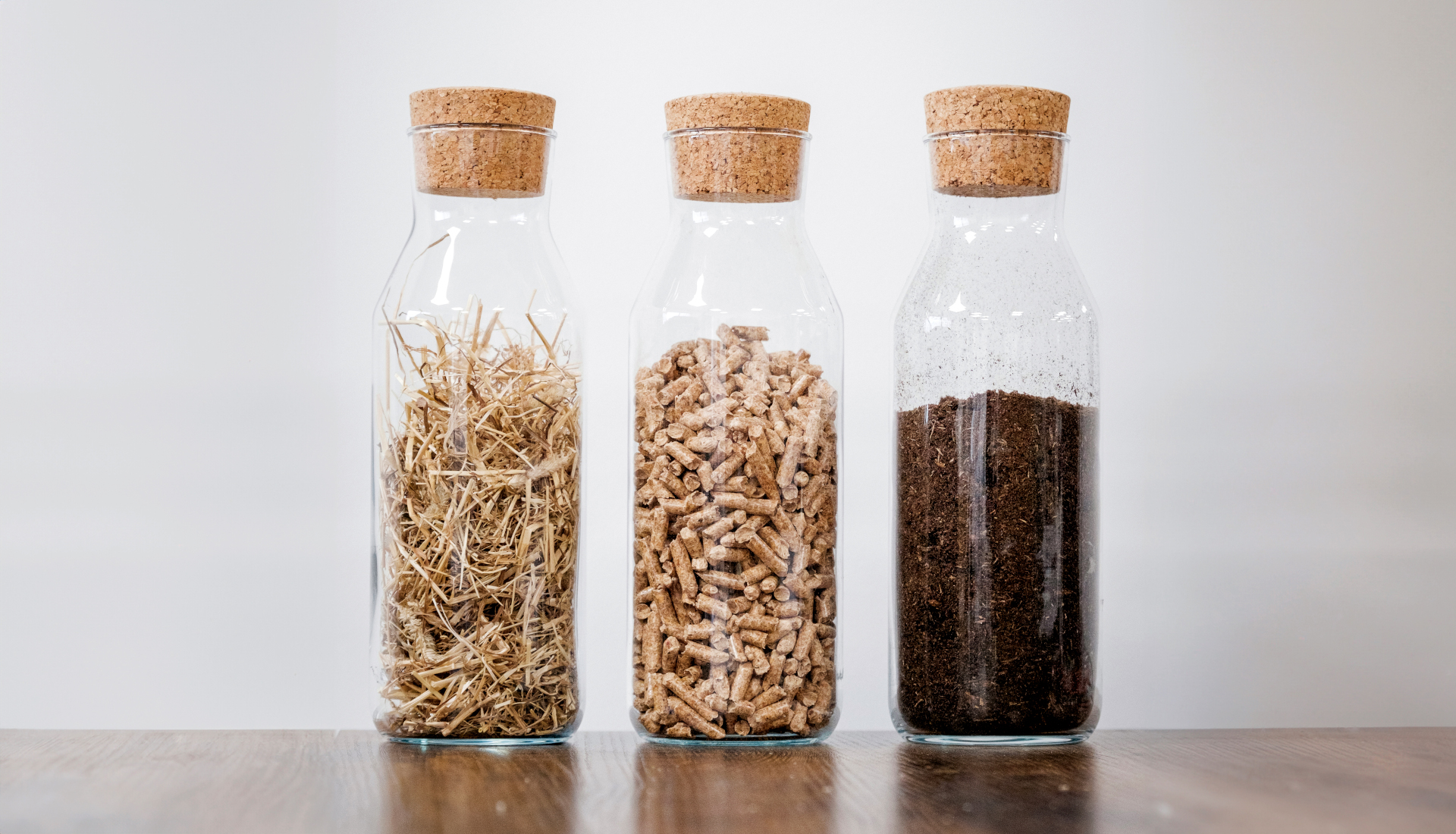
Assessing hydrogen purity … and by-product composition
The result of Wild Hydrogen’s biomass conversion process is a gas that is rich in hydrogen, but which also contains carbon dioxide, carbon monoxide, methane and a range of other volatile compounds at low concentrations. However, to make their reactor a viable commercial proposition, they need to produce gas that is high in purity and have an analytical system that can provide evidence of that purity.
The purity of their hydrogen, important as it is to the company, isn’t the end of the story. The gasification process also results in solid biochar and a small amount of liquid bio-oil (or tar). Understanding the chemicals present in these products is essential for working out the processes that are happening inside the reactor and thus optimizing the yield of hydrogen. But the team also has an eye on keeping the whole process as “circular” as possible by reusing these by-products: The biochar could be used for CO2 capture, for example, while the bio-oil could be added back into the feedstock to generate more hydrogen.
Understanding the composition of all these gases, liquids and solids needs a versatile analytical setup – and that’s where Shimadzu comes into the story.
Developing a bespoke analytical system
The conversation with Shimadzu started early on, following a meeting at a laboratory tradeshow event. The team at Wild Hydrogen was particularly excited by the possibility of covering the whole range of gaseous analytes in one run, and the decision to go with Shimadzu was cemented after realizing the value of Shimadzu’s consultative approach and once they’d seen firsthand the capabilities of their instrumentation.
Soon it was clear that a custom system was going to be needed, because the conditions within the reactor precluded using online sampling, while Wild Hydrogen’s desire to accommodate analyses of non-target compounds in liquid and solid fractions as well as gas samples meant that MS detection (rather than FID, TCD or BID) would be required.
Off-the-shelf systems for this kind of work aren’t readily available, but Shimadzu specializes in modifying standard GC-MS instruments for specific applications, so they set to work on devising a setup for Wild Hydrogen. The result was a bespoke system based on the Shimadzu GCMS-QP2020 NX, with the setup for gas analysis involving two sample loops filled from a canister or gas bag. The loops are connected to PLOT columns that provide excellent performance for hydrogen, carbon dioxide and the other permanent gases expected. The use of an MS detector means that the system can detect and identify the volatile organic compounds expected from the biochar and bio-oil, separating the mixtures achieved by simply replacing one of the PLOT columns by a capillary column.
Research Chemist Dr. Michael Sims
The system was installed in summer 2023, at roughly the same time that Dr. Michael Sims joined Wild Hydrogen as a Research Chemist. With his background in organic geochemistry, Michael was familiar with using pyrolysis to study organic residues in rocks, so the transition to studying the breakdown products of biomass in the company’s reactors using the new GC-MS was a natural step. In his current role, he’s working on their fourth reactor prototype, nicknamed “Mini”, with a focus on maximizing energy efficiency and recovering heat.
Versatile instrumentation and responsive staff
Having been using the Shimadzu system for nearly a year, Michael says he’s very happy with it: “What we like about it is its versatility – we can adapt the setup to run a number of different analyses, and it’s very simple to switch between them. If we’d just got a gas analyzer or an off-the-shelf GC-MS system, we wouldn’t have that ability.”
And having an in-house system means he can respond quickly to internal requests, because they don’t need to rely on expensive and time-consuming outsourced analyses. “With our Shimadzu system, I can run a gas analysis, and within 10 minutes I can tell the rest of the team what the composition is. It’s our laboratory workhorse, and it’s fair to say that it’s become a vital part of our operations.”
The level of service they’ve received from Shimadzu has been important to Michael and the rest of the team at Wild Hydrogen, he adds: “Getting the system up and running was seamless, and the aftercare has been very positive too – everyone’s really approachable, and if we have a question, however small, we can just get in touch.”
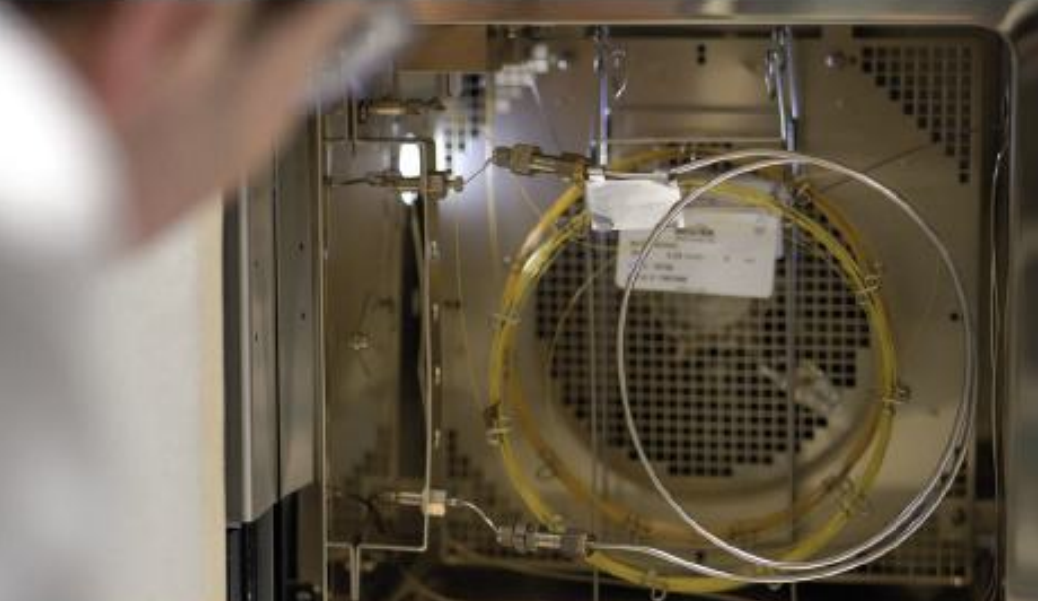
Leading the way in sustainable hydrogen
Currently, says Michael, they’re embarking on projects to investigate the best conditions for cleaning up their gases. The first aspect is downstream technology to separate out the CO2 from the hydrogen, followed by purification equipment.
For the hydrogen, Michael says a lot will depend on what is requested by the purchasers of their gases. “But”, he adds,“we’re basically aiming to generate hydrogen of sufficient purity suitable for the fuel cells used in hydrogen-powered vehicles.”
To ensure that the CO2 they separate out is of a suitable purity for carbon storage, they’ll need to check that it’s free from oxygen and other contaminants – another aspect of their workflow for which their Shimadzu system will no doubt prove very useful, he explains.
So, in conclusion, Wild Hydrogen are getting a lot of value from their Shimadzu GCMS. Michael says: “Having a versatile analytical system that provides quick sample turnaround has not only accelerated our R&D but it will be integral to verifying the purity of the gases we produce too.”
And those benefits will be crucial to helping Wild Hydrogen lead the way in the cost-effective, sustainable generation of “Clear Hydrogen” – a win-win for industry and the climate.