A guardian of purity
Determining trace amounts of sulfur compounds in hydrogen fuel with SCD
Omar Mayorga, Shimadzu Europa GmbH
By keeping the aim of carbon neutrality for 2050, hydrogen as fuel seems to have a big potential as it does not emit CO2 when burned. It is well known that if impurities of sulfur components are present in hydrogen, the catalyst of the fuel cell could be damaged. In case of sulfur compounds, the ISO 14687-2 norm defines a quantification limit of 4 ppb total sulfur. In this article, it is explained how it was possible to effectively measure sulfur compounds at a low ppb level by means of a Nexis GC-2030 with sulfur chemiluminescence detector (SCD) and a gas sampling valve. In addition, a MicroJet Cryo-Trap system allows to get excellent chromatograms, even considering the big amount of sample injected to the detector.
Hydrogen plays a key role as fuel in different fields of industry for the transformation from fossil energy towards green energy. It is considered a clean fuel when consumed in a fuel cell since it produces only water. Hydrogen can be produced from a variety of domestic resources, such as natural gas, nuclear power, biomass and renewable power like solar and wind energy. These qualities make it an attractive fuel option for transportation and electricity generation applications. It can be used in cars, in houses, for portable power and in many more applications.[1]
The different shades of hydrogen: grey, blue and green
Depending on the industrial production method, hydrogen can be categorized in three different groups: grey hydrogen, the most widely produced type of hydrogen which is derived from natural gas, the high ratio of CO2 being responsible for the “grey” designation to this hydrogen; blue hydrogen has a lower carbon dioxide impact on the environment because the carbon dioxide created in its manufacture is captured and stored; green hydrogen is produced in a completely different way: by electrolysis powered by renewable energies. This means that no harmful gases are created at any point in the production cycle. One of the most exciting things about green hydrogen is that it can be produced from water. Due to the abundance of water on planet Earth, it seems likely that green hydrogen could become a nearly limitless source of energy for all of us in the future.[2]
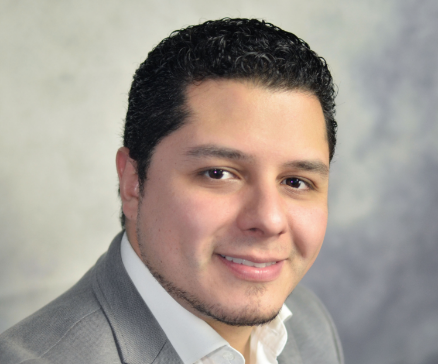
Omar MayorgaShimadzu Europa GmbH
How to keep hydrogen clear of contamination
Independent of the production route, contamination of hydrogen with various substances may occur that show degradation effects on the catalysts used in fuel cells, affecting the performance and limiting the lifetime. Among these are e.g. CO, CO2 and hydrocarbons but also organic sulfur species. While many of the adverse effects are reversible, sulfur compounds pose a special risk, being catalyst poisons leading to irreversible damage, as they form strong metal-sulfur bonds.[3] Using the Nexis SCD-2030 from Shimadzu, a next-generation sulfur chemiluminescence detection system, this risk is being reduced thanks to its enhanced sensitivity reliability. The highest stability in its class and excellent equimolar response yields truly reliable results and improved laboratory productivity.
To ensure efficient performance and maximum lifetime of fuel cells, hydrogen must fulfil the necessary purity levels, which are specified in ISO 14687:2019.[4] For sulfur species a quantification limit as low as 4 ppb total sulfur content is required, and the list of target compounds includes H2S, COS, CS2 and mercaptans. To reach this challenging requirement, a sensitive technique to determine sulfur content is necessary. In this study, a valve system connected to a gas chromatograph (GC) with sulfur chemiluminescence detection (SCD) is presented. To reach the quantification limit, sample focusing prior to detection was done with a cryogenic cold trap by using liquid nitrogen cooling (Figure 1).
Instrumentation
In this application, a valve system for gas sampling connected to a gas chromatograph (GC), model Nexis GC-2030, was used . Detection was performed by sulfur chemiluminescence detection (SCD) with a Nexis SCD-2030. To allow the analysis of big sampling volumes (20 mL) of highly volatile compounds, a valve GC system was built together with a cryogenic cold trap that used liquid nitrogen cooling for sample focusing prior to detection.
To avoid any adsorption, absorption and reaction of sulfur compounds, all tubing and valves were Sulfinert®-treated.
Furthermore, to ensure a high reproducibility for long-term measurements, the systems allow the injection of an internal standard (ISTD) which is done via an extra gas sampling valve. A fully schematic representation of the instrument used is shown in Figure 2.
Results
Carbonyl sulfide (COS) at different concentrations was analyzed. It was possible to create a calibration curve with the lowest concentration of 1.3 ppb which is much lower than the 4 ppb indicated in the ISO norm. This calibration curve showed a very good linearity within the range up to 12.9 ppb as can be seen in Figure 3.
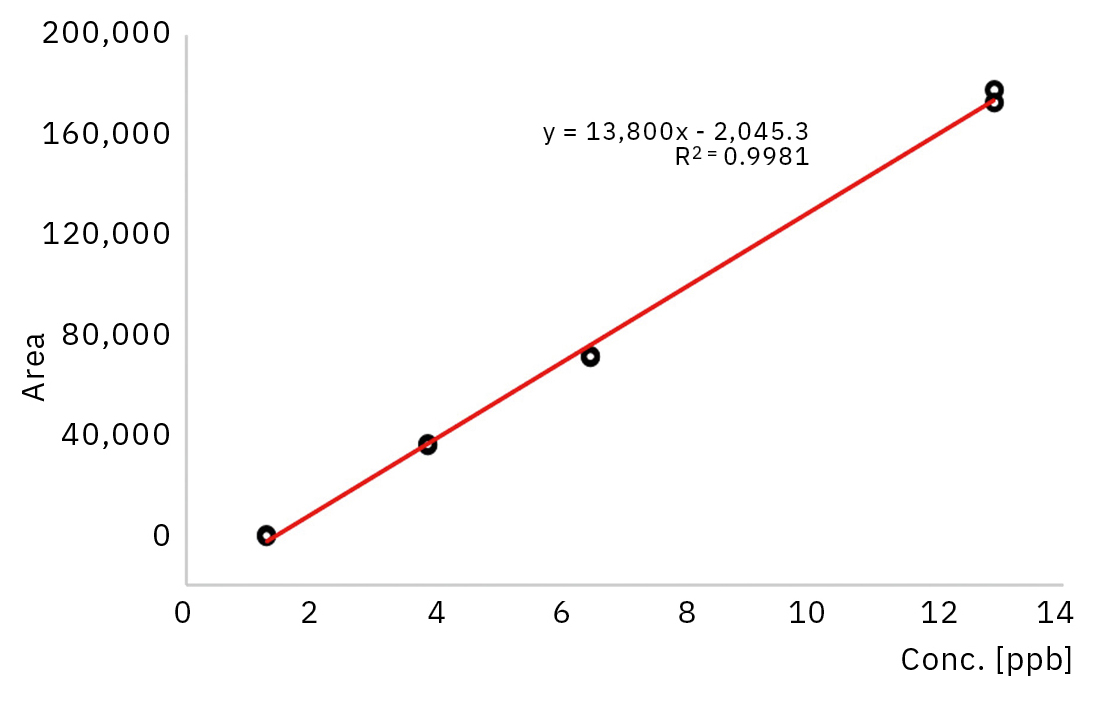
To determine reproducibility of the analytical method, a 3.9-ppb COS standard was injected ten times. Calculation of the relative standard deviation (%RSD) for peak areas and concentrations can be seen and revealed the reliability of the setup (Table 1). Both area and concentration reproducibility were below 2 %, ensuring reliable detection and quantitation of the sulfur compounds at low concentrations.
# |
Area |
Conc [ppb] |
1 |
51,151 |
3.879 |
2 |
50,914 |
3.861 |
3 |
52,193 |
3.958 |
4 |
51,838 |
3.931 |
5 |
51,800 |
3.928 |
6 |
50,768 |
3.850 |
7 |
50,815 |
3.854 |
8 |
50,716 |
3.846 |
9 |
50,557 |
3.834 |
10 |
50,300 |
3.814 |
Average |
51,105 |
3.876 |
%RSD |
1.23 |
1.23 |
To guarantee long-term stability, an internal standard addition was implemented to the system by using tert-butyl mercaptan (TBM). In this case, the same compound was analyzed as target. As observed in the chromatogram of Figure 4, TBM could be successfully quantified with a concentration of 1.07 ppb (first peak at around 6 min) as well as effectively used as internal standard (second peak at around 10 min).
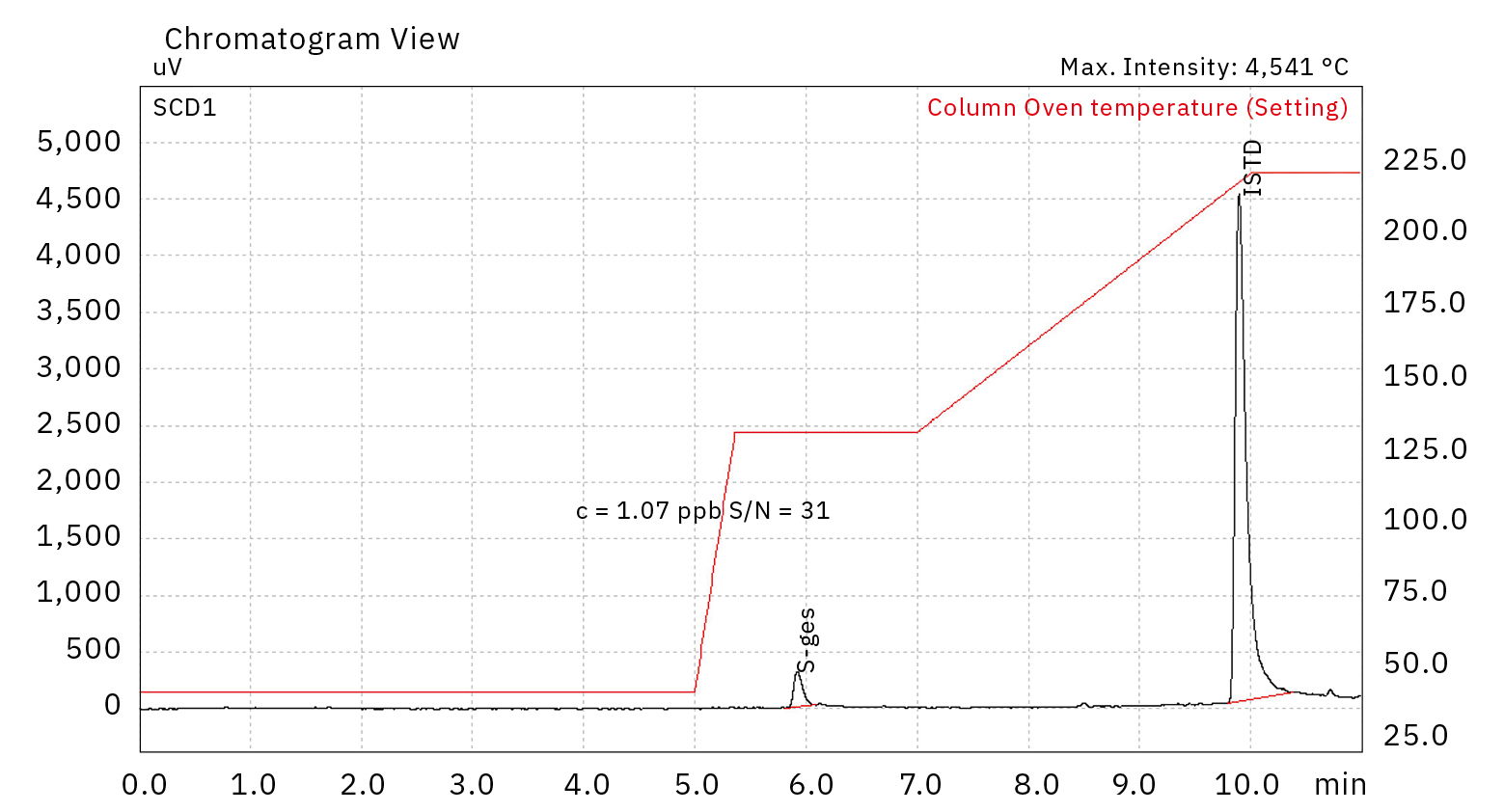
Paving the way for total sulfur compound quantification in hydrogen
The sulfur chemiluminescence detection using the Nexis SCD-2030 allows to selectively detect the total sulfur content in gases without the effect of hydrogen as matrix of the sample. Sulfur compounds can be determined with a quantification limit of less than 4 ppb, exceeding the requirements of ISO/DIS 14687 and DIN EN 17124. In the near future, the analysis of samples with more than one compound is planned and will corroborate the big potential of the system for total sulfur compound quantification in hydrogen fuel.
[1] Hydrogen Fuel Basics | Department of Energy
[2] Better Understanding of Green Hydrogen | Podcast | Siemens Energy Global (siemens-energy.com)
[3] Impeding Catalyst Sulfur Poisoning in Aqueous Solution by Metal–Organic Framework Composites – Zhou – 2020 – Small Methods – Wiley Online Library).
[4] ISO/DIS 14687(en) Hydrogen fuel quality Product specification, online available: iso.org/obp/ui/#iso:std:iso:14687:dis:ed-1:v1:en