Cosmetics – how clean is clean?
TOC-based cleaning validation
Anika Brett, Tilman Stellfeld, Mann & Schröder GmbH
In the cosmetics industry, Total Organic Carbon analysis (TOC) is a meaningful summary parameter for evaluating the cleaning efficiency of manufacturing plants and equipment. What is important to consider?
If cosmetics promise one thing besides beauty, it is cleanliness. The industry stands for hygienic care, well-being and many more pleasant and pristine characteristics. But how can we be certain both that consumers feel good and that the products themselves are good, i.e., of high quality and ultimately produced in compliance with the law? For this, the cosmetics themselves must be one thing in particular: clean. But what exactly does “clean” mean in this context?
All manufacturers of cosmetic products such as soaps, creams or makeup must ensure the cleanliness of the manufacturing facilities and equipment used. That said, how this is to be carried out and validated is only vaguely formulated in the corresponding regulations.[1] It is important that a standardized cleaning procedure exists and that the manufacturer can prove that the cleaning has been effective. The summary parameter Total Organic Carbon analysis (TOC) provides an overview of the cleaning efficiency. The process is also used at Mann & Schröder Cosmetics, a manufacturer of high-quality cosmetic products for over 65 years.
Applicable requirements for cosmetics manufacturers
According to DIN EN ISO 22716:2016 for cosmetic Good Manufacturing Practice (GMP), a suitable cleaning and, if necessary, disinfection program applies to all equipment. This also includes specified effective cleaning and disinfecting agents. The IFS HPC (International Featured Standard – Household/Personal/Care), an international standard for assessing products and processes of manufacturers and suppliers of household and personal care products, further defines the applicable requirements. According to these, the cleaning measures must also be validated accordingly and documented by means of a defined sampling plan using a suitable procedure. The type of validation, on the other hand, is not stipulated.
Both the pharmaceutical and food industries generally place even higher demands on cleaning as well as its validation than does the cosmetics industry. This is reflected in corresponding specifications and recommendations. Based on this, meaningful methods tailored to the individual case can be developed and a suitable validation procedure can also be defined for the cosmetics industry.
The TOC summary parameter
In cosmetic products, a large proportion of the ingredients consist of organic compounds; the same can be said for most cleaning agents. Therefore, TOC is a suitable parameter for checking the cleanliness of equipment following a production run. In order to determine a suitable cleaning and validation procedure, various cleaning steps are carried out and then the “final rinse water” is analyzed. This allows the efficiency of the cleaning to be determined and validated. Additionally, rinsing processes can be optimized in this way until they meet the requirements, thus cutting costs.
There are various techniques to determine the TOC. The most common is catalytic combustion oxidation. It oxidizes the carbon components at high temperatures using a platinum catalyst. As a result, the CO2 produced is detected with a nondispersive infrared (NDIR) detector.
Since inorganic carbon compounds such as carbonates and hydrogen carbonates are detected in addition to the organic compounds, two different TOC determination methods have been established to remove the inorganic compounds from the sample. In the most commonly used method, the so-called NPOC (Non Purgeable Organic Carbon) or direct method, the sample is first acidified using a mineral acid. It converts the inorganic carbon compounds to carbon dioxide and then a purge gas removes them from the sample. An aliquot of the prepared sample is then oxidized and the resulting CO2 is measured.
However, if cleaning agents that tend to foam are used for cleaning equipment, the NPOC method is often unsuitable. This is because the sample foams up anyway when the CO2 is degassed, so underestimation is likely. For these kinds of samples, the so-called difference method is ideal. First, the concentration of total carbon compounds (TC) is determined by oxidation. For this purpose, a part of the sample is completely oxidized – without sample preparation. The second step is to measure the inorganic carbon (IC) compounds. To this end, the carbonates and hydrogen carbonates are converted to CO2 by acidifying the sample and transported to the detector with the carrier gas. Using difference formation (TC – IC = TOC), the TOC concentration can be calculated.
Modern analyzers such as those from the TOC-L series from Shimadzu handle sample preparation (acidification and degassing) fully automatically. The systems operate with a highly effective platinum catalyst at a combustion temperature of 680 °C. The 680 °C combustion catalytic oxidation method was originally developed by Shimadzu and is now used worldwide. In addition to the direct method (NPOC), the Shimadzu systems can also determine TOC using the differential method. The devices have a special syringe unit that allows samples to be automatically diluted when the calibration range is exceeded as well as automatic dilution of standards to generate calibration curves even at equidistant concentration intervals.
0 % alcohol – really?
The required purity of the final rinsing step is determined by means of a risk assessment. Its goal is to ensure legally compliant products. A suitable scenario for risk assessment in the manufacture of cosmetics is the carryover of an ingredient from an ingredient-containing product to an ingredient-free product. Preservatives are a classic example of this. Certain products have explicit claims that refer to their specific composition, such as “free of preservatives”, “0 % alcohol” or “perfume-free” and this must be ensured during their manufacture. This means that the ingredient must not be detectable in the cosmetic product.
To calculate the TOC acceptance criterion, the first step is to define a risk-oriented indicator substance, in this case the carryover substance. A risk assessment of the production facilities is then used to determine the amount of rinse water from the final rinse that remains in the production vessel in a worst-case scenario and which would then lead to the subsequent production batch becoming contaminated. In this case, “worst case” means the largest possible amount of rinsing water is carried over to the smallest possible subsequent batch.
The next step is to determine the maximum concentration of the lead substance that may be contained in the amount carried over in order not to exceed the detection limit in the subsequent preparation. The resulting TOC content in the final rinse can then be calculated from the detection limit and the amount of carbon carried over using the number of carbon atoms in the indicator substance and the molar masses of the indicator substance and carbon (Figure 2). In the context of this observation, it is assumed that this TOC concentration results exclusively from the leading substance.
Once the acceptance criterion is defined, validation can begin. Samples are taken at various rinse cycles and analyzed for TOC content. As you would expect, the TOC content decreases with each rinsing step (Figure 3). The cleaning process must be considered separately for each manufacturing plant and each product group. Table 1 displays the TOC readings of different products in the same manufacturing plant after running the same cleaning program. The measured values differ significantly depending on the product type. If compliance with the specified acceptance criterion is confirmed, even after repeated performance, the cleaning method is considered validated for the respective product.

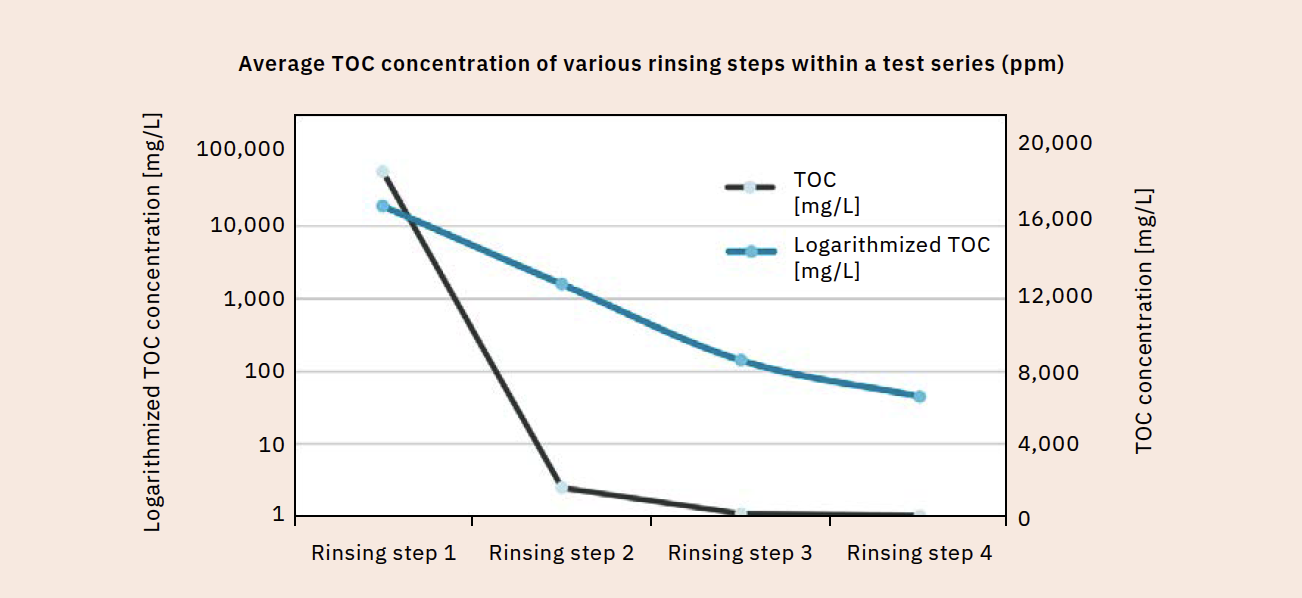
MS Parameter |
Hair perfume |
Sun spray |
Hairspray |
Facial toner |
TOC in rinsing step 1 [ppm] |
7,187 |
14,350 |
5,521 |
4,928 |
TOC in rinsing step 2 [ppm] |
189 |
5,785 |
1,102 |
159 |
TOC in rinsing step 3 [ppm] |
19 |
2,148 |
50 |
36 |
TOC in rinsing step 4 [ppm] |
44 |
In the cosmetics industry, TOC is a meaningful parameter for evaluating the cleaning efficiency of manufacturing plants and equipment. It makes analysis simple, accurate and fast. In addition, modern analyzers such as Shimazdu’s TOC-L carry out the necessary sample preparations automatically. Precision measurements can also help to optimize the cleaning steps and, in this way, reduce costs and the use of resources.
References/further information
Cosmetics GMP (DIN EN ISO 22716:2016); IFS-HPC
International Featured Standard – Household/Personal/Care DIN EN ISO 22716