How to create a nervous system for infrastructural buildings
Design and testing of distributed optical sensors and other diagnostic solutions
Kamil Badura, Tomasz Howiacki,
SHM System/Nerve-Sensors
Today, societies require an intelligent infrastructure capable of detecting threats and equipped with early warning systems. Though built to last, collapsing buildings and infrastructure is a common occurrence throughout the world. Diagnosing civil engineering and geotechnical facilities is therefore absolutely mandatory in order to avoid damage and save human lives. One of the most promising approaches is the use of monolithic fiber optic sensors that are fully integrated into a given structure, providing strain, displacement, temperature or vibration monitoring continuously over its entire length – from millimeter to kilometer range!
The collapse of the Ponte Morandi highway bridge in Genoa in 2018 made big news and seemed like a singular event, but the collapse of infrastructural buildings is not that seldom. Many buildings and bridges break down every year, many due to structural failure from ageing infrastructure. And not all buildings are built alike. Modern infrastructure is usually designed with non-standard geometry, using new materials and advanced structural solutions. On the other hand, ageing infrastructure requires appropriate maintenance to ensure an adequate level of safety. Therefore, knowledge of the mechanical and thermal behavior of the structure under normal operating conditions is essential for assessing its technical condition and thus for optimal decision-making.
Responsibility for the surrounding infrastructure leads to the search for effective solutions that can benefit society as a whole. Firstly, proper monitoring can help prevent the failure or catastrophe of safety-critical engineering structures, which directly translates into the protection of human health and life. Secondly, it leads to economic, environmental and social benefits. It is also important to note that the knowledge gained from field conditions contributes to a better understanding of the phenomena occurring in nature and in engineering, thus improving our theoretical models and optimizing future solutions.
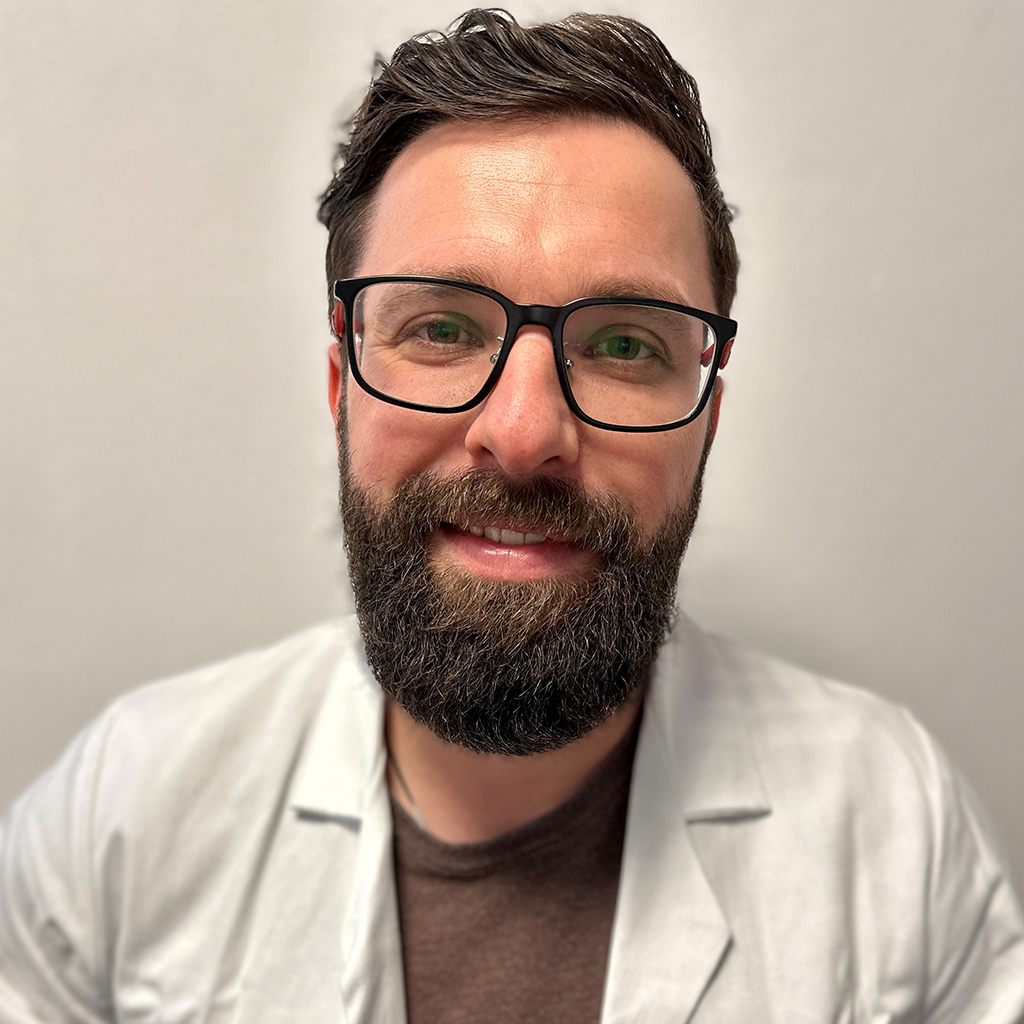
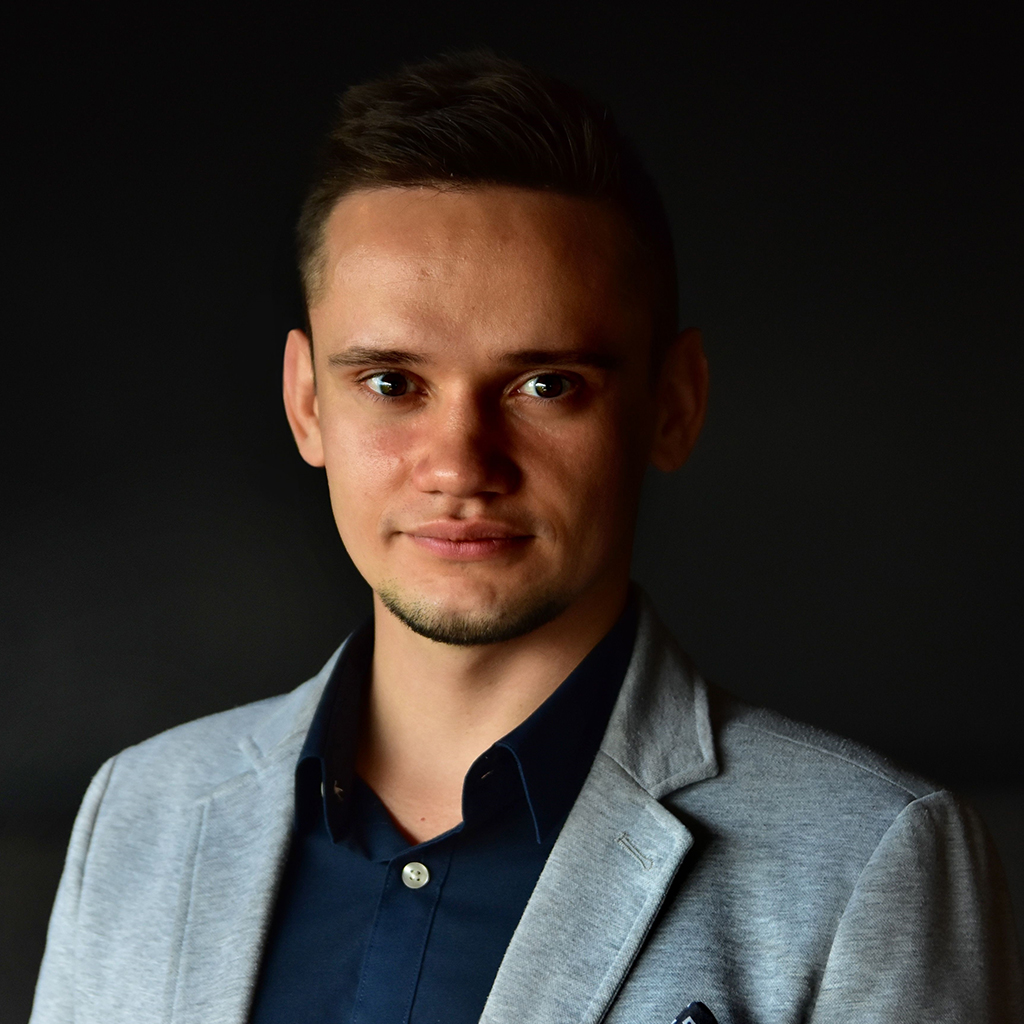
Monolithic fiber optic sensors – a nervous system for structures
Among the many measurement techniques available on the market, there is a constant search for the optimum solution in terms of diagnosing civil engineering and geotechnical facilities. One of the most promising approaches is the use of monolithic fiber optic sensors that are fully integrated into a given structure, providing strain, displacement [1], temperature or vibration monitoring continuously over its entire length [2] – from millimeter to kilometer range! This means that instead of a single number obtained at the location of the gauge, we get the continuous profile of the measured quantities, allowing us to detect anomalies or local events such as cracks [3], stress concentrations or other damage.
Despite the undeniable benefits of distributed fiber optic sensing (DFOS) technology, it is not a “plug and play” solution. There are several aspects that need to be carefully considered and planned prior to measurement. These include the type of the sensors and their parameters like diameter, elastic modulus, external surface or internal design. Nerve-Sensors as a department within SHM System is engaged in the design, development and research of worldwide unique monolithic sensors for DFOS.
Initial market research in 2015 showed that there were no alternatives for layered sensing cables used in field applications. This solution was well-known from telecommunications, where optical sensing fibers are protected by a set of multiple layers. However, from a measurement point of view, they were limited by several drawbacks. Firstly, the use of plastic and steel components with low elastic range meant that the cables were destroyed very quickly. Secondly, the intermediate layers disturbed the strain transfer mechanism due to the slippage effect. Finally, the smooth outer surface did not provide adequate adhesion to the surrounding material.
A pioneering innovation, inspired by human design
There was no solution on the market designed directly for civil engineering and geotechnical monitoring. To fill this gap, the Nerve-Sensors family has been developed to overcome the existing limitations. The new sensors consist of a monolithic core without layers, which ensures the most accurate strain measurements. Plastic and steel components have been replaced with highly elastic composite materials. External braiding improves the bonding quality between the sensor and the surrounding material, e.g. concrete or soil. Monolithic sensors are designed to be integrated into a structure similar to the human nervous system [4], and this was the main idea behind the proposed name for the family.
Calibrating for effectiveness and accuracy with Shimadzu testing machines
Monolithic sensors are taking structural health monitoring (SHM) to a new level, but their effectiveness and accuracy had to be verified in precise and rigorous laboratory tests to remove any doubt about their behavior. That is why SHM System’s laboratory was equipped with two Shimadzu testing machines:
AGS-50kNX and AGX-V-300kN (Figure 1). Both are used for precise mechanical testing of different types of monolithic sensors, for example stiff and robust EpsilonRebar or flexible and versatile EpsilonSensor (Figure 2). The main specifications that need to be analyzed include the strain accuracy and maximum strain range. Thanks to the special composite core, EpsilonSensor has the widest measuring range on the market at up to 4 % (Figure 3), which is as much as four times the typical range of layered cables. This opens up new possibilities for analyzing the condition of structures, including the measurement of local cracks and fractures that cannot be reached by competing solutions.
Shimadzu’s testing machines are in continuous use, not only to analyze large numbers of samples for statistical findings but also because the Nerve-Sensors family is constantly evolving, with new, improved solutions being designed and tested to meet specific market needs. Materials, cross-sections or external surface characteristics change in time. For example, the addition of graphite improves the thermal conductivity of the temperature sensor, and the rectangular cross-section makes it easier to mount on flat surfaces. Appropriate testing is required each time.

Providing old structures with new sensory intelligence
In practice, the distributed sensing approach is often complemented by spot diagnostic solutions. These are also developed and tested in the SHM System laboratory. Two of these are highlighted hereafter. The first solution is called the plastic deformation sensor (PDS) and is the world’s first and only sensor capable of detecting steel yielding without any knowledge of material properties, initial stress-strain state and actual technical condition. It is not only suitable for diagnosing steel structures but also for detecting the near-to-failure state of other materials such as concrete. The sensor can be made using different measurement technologies like optical fibers (Figure 4), foil strain gauges (Figure 5) or vibrating wire sensors (Figure 6). It can therefore be easily integrated into existing monitoring systems. Thanks to the special calculation algorithm, this is an excellent tool for both new and existing ageing infrastructure with unknown deformation state and lack of documentation.
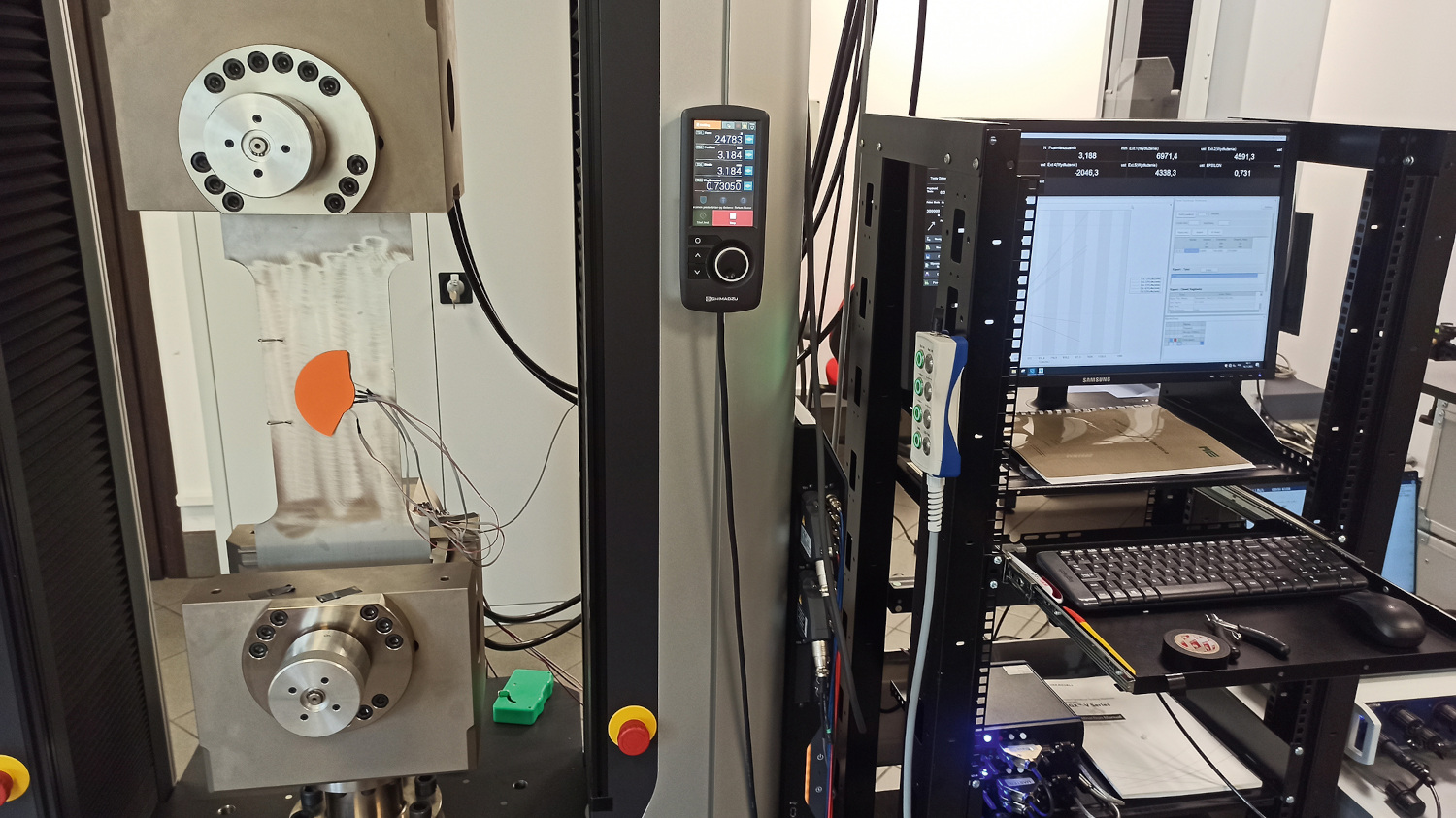
The second unique solution relates to fiber bragg gratings (FBGs), one of the most commonly used fiber optic spot gauges. Unfortunately, standard FBGs have a limited strain range and are only suitable for measuring uniform materials, usually within their elastic behavior. Large deformations in inhomogeneous materials such as concrete (local effect of aggregate or cracks), composite textiles (disturbance by perpendicular fibers) or simply steel working in a plasticized state cause standard FBGs to split the spectrum, and further measurement is no longer possible. The new FBG sensor developed by the specialists at SHM System overcomes these limitations and allows the measurement range to be significantly extended, thus increasing the range of possible applications.
Both the new PDS and the new FBG are installed on different samples of different materials and then tested on the Shimadzu machines. The machine’s acquisition system is synchronized with the tested technologies to provide reliable reference data. For example, the PDS coefficient calculated from the raw strain data is compared with the force values recorded by the Shimadzu testing machine (Figure 7) to assess the effectiveness of the PDS in determining the yield time.
A dream only a few years ago, today a life-saving innovation
It must be emphasized once again that the failure consequences of civil engineering and geotechnical facilities include not only financial, social and environmental losses but also loss of human health or life. In order to preserve human life, the team from SHM System & Nerve-Sensors went full circle and took inspiration from human life: the human nervous system, perfect in terms of hazard identification and early warning. It served as an unsurpassed model to develop a diagnostic system for engineering and geotechnical structures. The linear composite sensors, fully integrated into the structure, are designed as the nerves responsible for detecting threats, while the data logger is the brain that processes, visualizes and interprets the data. This bold vision was only a dream a few years ago but is now a reality on hundreds of bridges [5] and other engineering facilities around the world saving structures and most importantly – human lives.
[1] Bednarski, Ł., Sieńko, R., Grygierek, M., Howiacki, T. (2021). New Distributed Fibre Optic 3D Sensor with Thermal Self-Compensation System: Design, Research and Field Proof Application Inside Geotechnical Structure. Sensors. 21: 5089. https://doi.org/10.3390/s21155089.
[2] Piątek, B., Howiacki, T., Kulpa, M., Siwowski, T., Sieńko, R., Bednarski, Ł. (2023). Strain, crack, stress and shape diagnostics of new and existing post-tensioned structures through distributed fibre optic sensors. Measurement. 221: 113480. https://doi.org/10.1016/j.measurement.2023.113480.
[3] Howiacki, T., Sieńko, R., Bednarski, Ł., Zuziak, K. (2023). Crack Shape Coefficient: Comparison between Different DFOS Tools Embedded for Crack Monitoring in Concrete. Sensors. 23: 566. https://doi.org/10.3390/s23020566.
[4] Bednarski, Ł., Sieńko, R., Howiacki, T., Zuziak, K. (2022). The Smart Nervous System for Cracked Concrete Structures: Theory, Design, Research, and Field Proof of Monolithic DFOS-Based Sensors. Sensors. 22: 8713. https://doi.org/10.3390/s22228713.
[5] Howiacki, T., Sieńko, R., Bednarski, Ł., Zuziak, K. (2023). Structural monitoring of concrete, steel, and composite bridges in Poland with distributed fibre optic sensors. Structure and Infrastructure Engineering. 1–17. https://doi.org/10.1080/15732479.2023.2230558.