Some are important, some are toxic: Heavy metals are a natural part of the earth’s crust and also accumulate in plants through the absorption of water and nutrients. As a result, they can also end up in food, pharmaceuticals, cosmetics and other plant-based products. That’s why continuously monitoring raw plant materials is extremely important in order to prevent contamination and damage to health caused by toxic heavy metals. Both the ICP-OES and ICP-MS are fast, robust techniques.
Raw plant materials have always been the foundation of many different products, and “going plant-based” is in trend at the moment. Especially when it comes to gentle cosmetics or health products, consumers are turning back to the power of nature more and more. Plant-based products convey the idea of natural care and purity. However, the natural ingredients can literally have these heavy metals “in them”, as they accumulate in plants through the absorption of water and nutrients and eventually enter the human body. While some metals such as manganese and iron are essential for us as trace elements, others – such as cadmium or mercury – are toxic and can lead to long-term damage if ingested on a regular basis.
Heavy metals are everywhere. They occur in the soil and enter the environment through natural processes such as weathering, but human influences play a role here too. Usually, when heavy metals occur naturally in fields and bodies of water, the amount is so low that they pose no danger.
It is precisely the man-made deposits of heavy metals that lead to harmful contamination. They can enter the soil in various ways. For example, centuries-old mining and metallurgical waste, i.e. slag or ash, can still cause problems as contaminated sites. The disposal of this kind of waste has only been regulated by law since the end of the 20th century, which is why mining and metallurgical waste that has been carelessly dumped in the environment for centuries is still lying dormant in the soil. Since heavy metal pollution does not break down naturally, even this waste – despite being buried for hundreds of years – is just as dangerous today as it ever was.
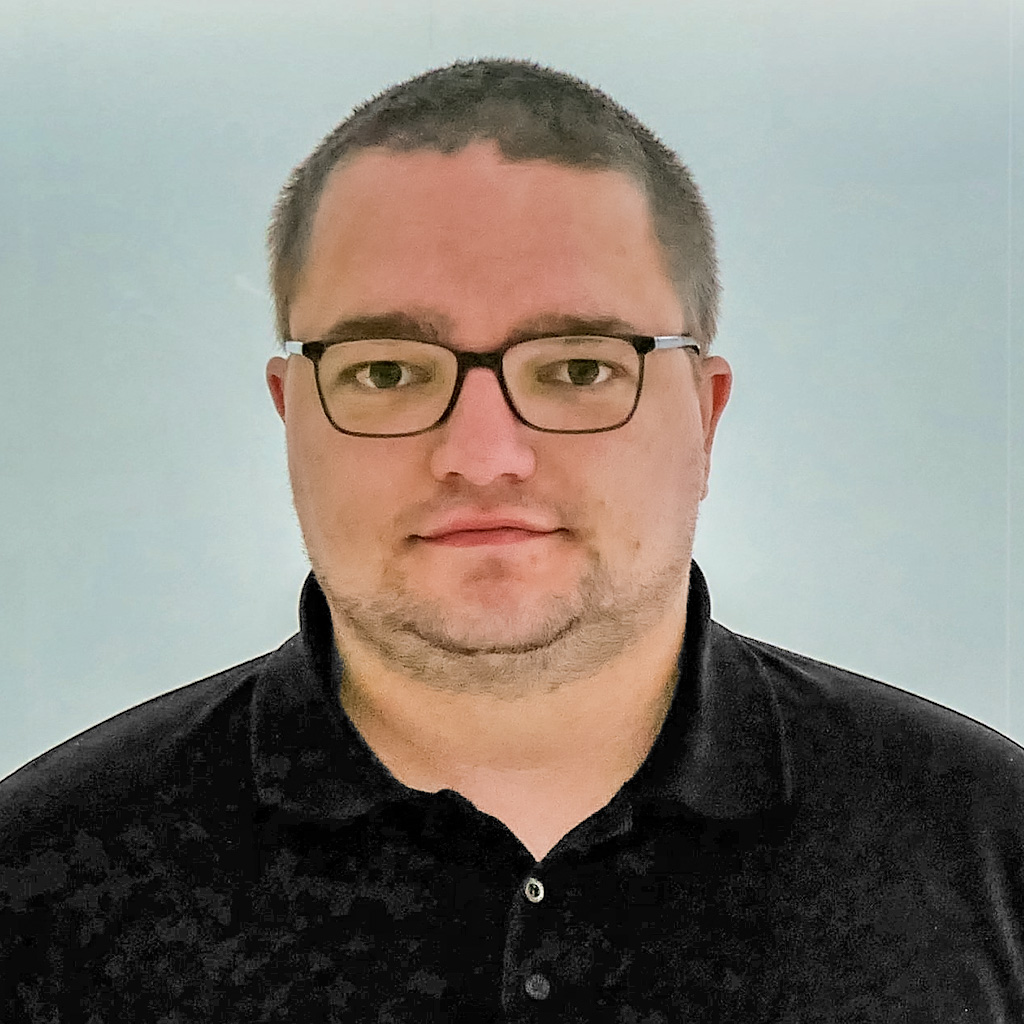
The use of sewage sludge as a fertilizer can also lead to contamination – chromium is one example here. There are legal regulations governing the use of sewage sludge as a fertilizer with regard to its composition and the maximum quantity that may be applied. However, if this type of fertilizer is continually used, then it can accumulate in the soil and become a long-term source of contamination.
Contamination with toxic heavy metals, even in small traces, can have dangerous effects. That’s why raw plant materials must undergo heavy metal analysis before being processed further. This places a variety of demands on laboratories and the respective measuring instruments, since the limit values are very low. The ICP-OES and ICP-MS techniques are perfect for this.
The ICP-OES, the all-rounder
Inductively coupled plasma optical emission spectrometry (ICP-OES) is a widely used method in element analysis and is primarily set apart by its speed and robustness. Up to 60 elements can be analyzed at the same time, covering a wide range from the ppb to the % range. This makes the ICP-OES technique one of the most widely used measurement techniques in the field of heavy metal analysis. By automatically switching between axial and radial measuring modes, macroelements such as calcium and magnesium can be measured together with trace elements such as cadmium in a single measuring cycle. The device doesn’t need to be adjusted for this, as the viewing direction is changed automatically and quickly using mirrors. This makes working with the ICP-OES very user-friendly and efficient. On top of this, the ICP-OES has the huge advantage of always being able to measure the entire spectrum, meaning qualitative measurements can also be carried out.
Raw plant materials must first be converted into a liquid measuring solution for analysis. The easiest way to do this is by microwave digestion, where 0.5 g of dried sample is mixed with 7.5 mL nitric acid (HNO3) and 0.5 mL hydrochloric acid (HCl). Then the solution is topped up to 25 mL.
As an example, six plants whose raw materials are used in naturopathy and in the food and cosmetics industry were analyzed for their trace element (heavy metal) content. As well as this, the macro elements were also determined in one example, the ICPE-9820 from Shimadzu being used (Table 1, Figure 1).
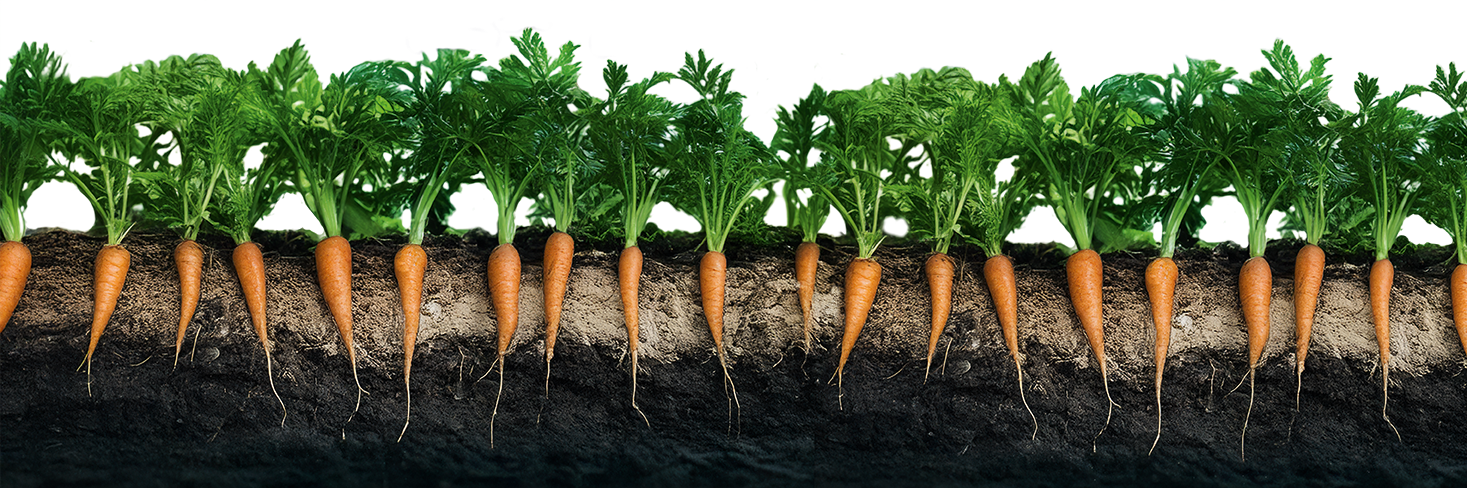
On the one hand, quantitative measurements of trace elements were taken using the calibration line method and, on the other, qualitative measurements for various macroelements such as magnesium, potassium and phosphorus. These are also particularly interesting to know about in relation to raw plant materials, for example as a quality feature in the food supplement and pharmaceutical industries.
The fact that both can be combined in a single measuring process is a huge advantage here. The complete spectrum from 167 nm to 800 nm is always recorded, so that qualitative evaluations can be made later.
The quantitative analysis of arsenic, cadmium, chromium, copper and lead showed that the samples of raw plant materials that were tested did not exceed the maximum levels recommended by the World Health Organization (WHO) (Table 2). In the EU, there are different limit values for raw plant materials depending on where they are used, which must be taken into account and which are set out in EU Regulation 2023/915, for example.
As [ppm] | Cd [ppm] | Cr [ppm] | Cu [ppm] | Pb [ppm] | |
Cardamom | < 0.2 | 0.06 | < 0.02 | 5.4 | 0.3 |
Cinnamon | < 0.2 | < 0.007 | 0.4 | 6.6 | 0.6 |
Goat weed | 0.4 | 0.13 | 2.8 | 4.5 | 1.5 |
Carrot | < 0.2 | 0.03 | 0.04 | 5.0 | < 0.1 |
Rehmannia root | < 0.2 | < 0.007 | 0.4 | 3.8 | < 0.1 |
The qualitative measurement (Table 3) is suitable for internal quality controls and checks. It is also often used to detect unknown contamination, which can then be quantified.
Ca [wt%] | K [wt%] | Mg [wt%] | Na [wt%] | P [wt%] | S [wt%] | |
Goat weed | 3.7 | 1.1 | 0.35 | 0.008 | 0.31 | 0.45 |
RF output | 1.2 kW |
Plasma gas | 8 L/min |
Auxiliary gas | 1.1 L/min |
Carrier gas | 0.7 L/min |
Distance between torch cones | 5 mm |
Integration time | 2 s |
The ICP-MS, for maximum sensitivity
Depending on the requirements, the sensitivity of ICP-OES technology may not be sufficient, which is why inductively coupled plasma mass spectrometry (ICP-MS) is becoming more and more important when it comes to monitoring raw plant materials.
Monitoring heavy metal residues in cannabis is a very topical issue here. The so-called Big Four (cadmium, lead, mercury and arsenic) are currently monitored with strict limits to protect consumers from health risks.
The high sensitivity of the ICP-MS enables detection/analysis limits down to the ppt range (parts per trillion). The large linear operating range extends into the sub-ppm range. As with the ICP-OES, both purely quantitative measurements and qualitative screening can be carried out.
Samples are also prepared using microwave digestion here with the addition of a nitric acid-hydrochloric acid mixture. The method parameters applied are shown below in Table 4. The ICPMS-2050 LF from Shimadzu was used (Figure 2).
The results in Table 5 were generated from the exemplary analysis of a cannabis sample.
On the one hand, this shows that the legal limits were not exceeded, on the other hand, the traces of heavy metals found in low concentrations prove just how sensitive the ICP-MS is.
As [ppm] | Cd [ppm] | Pb [ppm] | Hg [ppm] | |
Untreated cannabis | < 0.04 | 0.13 | 0.138 | < 0.015 |
Legal limit value | 0.2 | 0.2 | 0.5 | 0.1 |
Rest assured thanks to sensitive measuring methods
Whether it be various herbs in pharmaceutical or cosmetic products, ingredients for food or cannabis products: Raw plant materials are the foundation of many different products and are currently in particularly high demand due to the trend towards more natural ingredients. But just because something is a natural ingredient doesn’t mean it is always healthy and pure. Contamination with trace amounts of heavy metals can have dangerous effects on humans and the environment.