“There’s an easier way” – rethinking mass spectrometry
Innovative ion source overcomes limits in analysis
Petra Romero, Plasmion GmbH
Jan-C. Wolf, founder of Plasmion GmbH, was driven by the idea of making mass spectrometry more accessible, simpler and more efficient as early as his university days. He has made huge strides in this area with the development of the SICRIT® ion source: This universal innovation makes mass spectrometry more user-friendly, more powerful and more sustainable.
The vision of more accessible mass spectrometry
Even back when he was studying at the TU Munich, Jan-C. Wolf was already heavily involved in developing instruments and methods, particularly mass spectrometers. He quickly realized that the specific dependencies between separation and MS-based detection, i.e. the historically driven technical delimitation between GC-MS and LC-MS, result in a complexity that makes laboratory processes laborious and time-consuming. Wolf was convinced: “There must be an easier way!” This conviction stayed with him into his postdoctoral years at ETH Zurich. There he worked with Prof. Renato Zenobi, Professor of Analytical Chemistry at the Laboratory of Organic Chemistry, on developing what’s called an ambient ion source. The aim was to create a technology that allows volatile organic compounds (e.g. fragrances, flavorings or chemical warfare agents) to be analyzed on-site.
With the SICRIT® (Soft Ionization by Chemical Reaction in Transfer) technology, Wolf has developed an almost universal ion source for mass spectrometry. The potential quickly became obvious, and his colleagues at the institute wanted to use this new technology themselves – the business idea for Plasmion was born. The Augsburg-based company has been distributing the SICRIT® technology since 2018 and has been an official partner of the Shimadzu Corporation since this year. Shimadzu and Plasmion work together on projects in the areas of marketing and sales as well as in the field of research, where they jointly test the possibilities and limits of the ion source in combination with various Shimadzu devices.
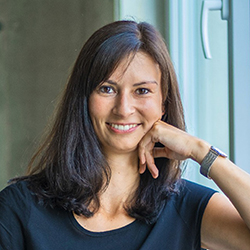
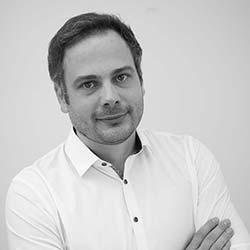
How the SICRIT® ion source works
The principle of the SICRIT® ion source is very simple: The source is mounted directly on the atmospheric pressure inlet of the (LC) mass spectrometer in just a few simple steps (plug & play). During mounting, the existing source is removed, a special adapter is attached to the inlet of the mass spectrometer and the source is simply “clicked on” with a ball lock, creating a gas-tight connection between the source and the device’s vacuum. Volatile or vaporized substances are drawn in by the vacuum and ionized on their way into the system by means of a cold plasma ring in the source. This form of ionization is efficient, comparably soft as electrospray ionization, but covers almost the entire chemical polarity range (from amino acids to alkanes), since SICRIT® can ionize both non-polar (typical GC) and polar (typical LC) analytes thanks to its unique ionization mechanism.
However, this technology has one limitation: What cannot be vaporized or transferred into the gas phase cannot be measured. This includes very large molecules such as proteins. Another aspect that hinders the analysis of large molecules is the fact that this form of ionization does not generate multiple charges on the analyte: In contrast, in electrospray ionization the standard ionization method for large molecules, several charges are formed and “attached” to the analyte via atomization. This reduces the analyte with the exemplary mass of 100,000 m/z and 20 attached charges to the m/z value of 5,000, thereby bringing it within the detectable mass range of the mass spectrometer.
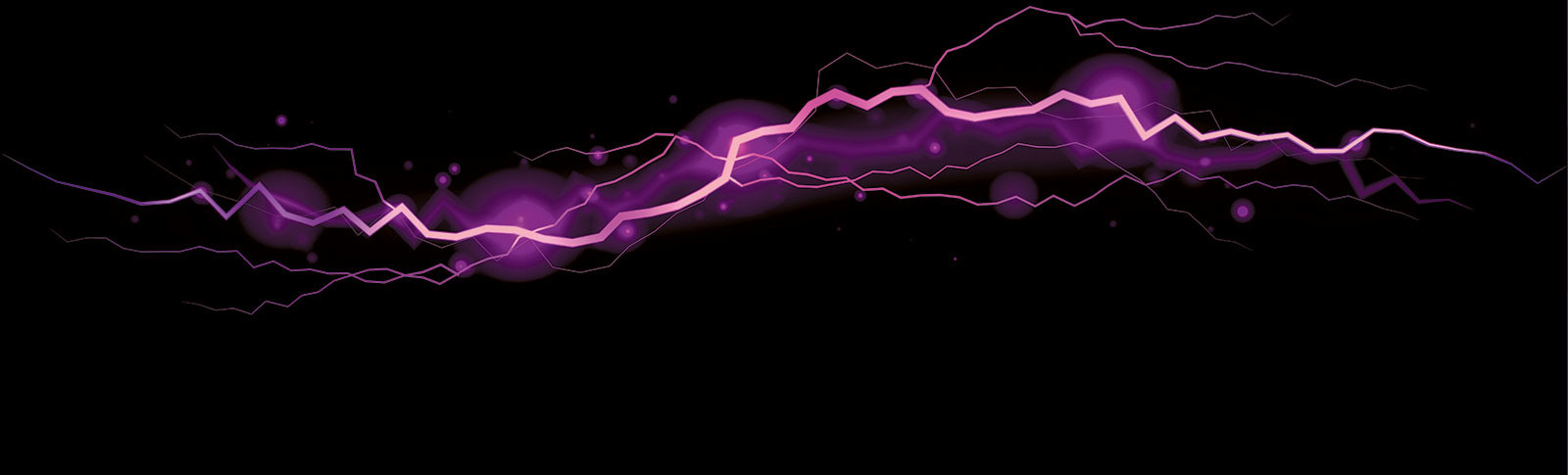
Numerous combination options
A major advantage of the SICRIT® ion source is its versatility. In addition to direct MS measurement, various modules enable all common chromatographic methods and dedicated MS instruments, such as gas chromatography (GC), liquid chromatography (LC) and supercritical fluid chromatography (SFC), to be combined with one (LC-)MS device.
Certain analyses that previously had to be carried out using different chromatographic methods can now be performed on a single LC-MS device, which to some extent removes the traditional separation between LC-MS and GC-MS markets.
Users benefit from high-resolution GC-MS – combining an LCMS-9030 Q-TOF with a GC (Figures 1 and 2), for example, creates one of the most powerful analysis systems on the market: A system that brings together the strengths of a GC (non-polar analytes and high separation performance) with those of an LC-MS (higher resolution, polar analytes). In this setup, the SICRIT® ion source acts as a link that connects the two analysis methods via the ionization range (non-polar/polar) and softness. This system has the potential to rethink mass spectrometry in terms of making chemical analyses easier and more sustainable with better results.
Overcoming limits for easier analysis
An obvious example of this is pesticide analysis, as the complexity of their chemical composition means pesticides have to be analyzed using both GC-MS and LC-MS. Therefore, laboratories need to employ several devices and workflows for an overall picture. At present, the Plasmion team is leveraging the unique ionization range of SICRIT® to develop a comprehensive GC-based pesticide method that reduces this effort in the future. The most important prerequisite for such a consolidated method is that it must be able to comply with the specified limit values (LODs). For this purpose, 74 LC-compatible pesticides from three standards (Restek GmbH) – organophosphorus compounds, organonitrogen compounds and hydramethylnon – were analyzed in a first set using GC-SICRIT®-Q-TOF (Shimadzu LCMS-9030) (Figure 3).[1] Here, a dilution series from 1 to 1,000 ng/mL was prepared in toluene, applied via 1 µL splitless injection and measured in triplicates. An HP-5ms column was used with hydrogen as the carrier gas.
The results show that the GC-SICRIT® method enables reliable detection of pesticides that are highly problematic in LC-MS, such as Folpet, while adhering to the specified LODs of the European Union.
Improved sustainability thanks to combined benefits
SICRIT® is based on mass spectrometers with atmospheric pressure inlet (AP-MS), which have more powerful pumps compared to conventional GC-MS systems. This allows considerably higher flow rates (up to 200 mL/min) of hydrogen to be used in GC coupling. As with the development of UHPLC, this now allows analysis times to be significantly reduced. Switching from helium to hydrogen alone already provides a speed advantage of 40 % (Figure 4). By using higher flow rates, the analysis time can be reduced by more than 80 %. Using hydrogen as a carrier gas is even associated with better sensitivity – in contrast to the loss of sensitivity of hydrogen when combined with electron impact ionization (typical for GC-MS). The hydrogen can be produced directly from water and electricity using a generator, making it much more sustainable than helium, which is now a scarce resource.
Out-of-the-box thinking for better results
Coupling GC with LC-MS also brings advantages in the areas of pharmaceutical quality control. The sensitive ionization, together with the excellent separation performance of gas chromatography, enables the direct identification of impurities in pharmaceuticals as well as ultra-trace detection of carcinogenic compounds such as nitrosamines. A respective application using an LCMS-9030 SICRIT®-GC coupling has shown to be one of the most sensitive nitrosamine applications on Shimadzu LC-MS instruments.
The unusual coupling makes the results difficult to compare with existing analyses. Comparing them to a corresponding analysis published by Shimadzu, which was carried out on the same device but with an APCI source (the standard ionization method for nitrosamines) and an LC, this unusual coupling via the SICRIT® source increases sensitivity up to a factor of 40, though (Figure 5).[2]
Efficiency meets sustainability – a paradigm shift in the laboratory world
The efficient use of our resources and the application of more climate-friendly analytics are challenges that every laboratory, from quality assurance to research and routine analysis, will have to face in the future. The SICRIT® ion source offers the opportunity to rethink and redesign established processes – not only to improve analytical efficiency but also to enhance sustainability by reducing analysis times, savings on equipment, and replacing scarce resources such as helium. This represents a real benefit not only for laboratories but also for the environment and ultimately for us all.
In the spirit of the inventor Jan-C. Wolf: “There’s an easier way.” – and it’s actually better.